Surf Blocks turn surfboard waste into fire-resistant homes on Maui
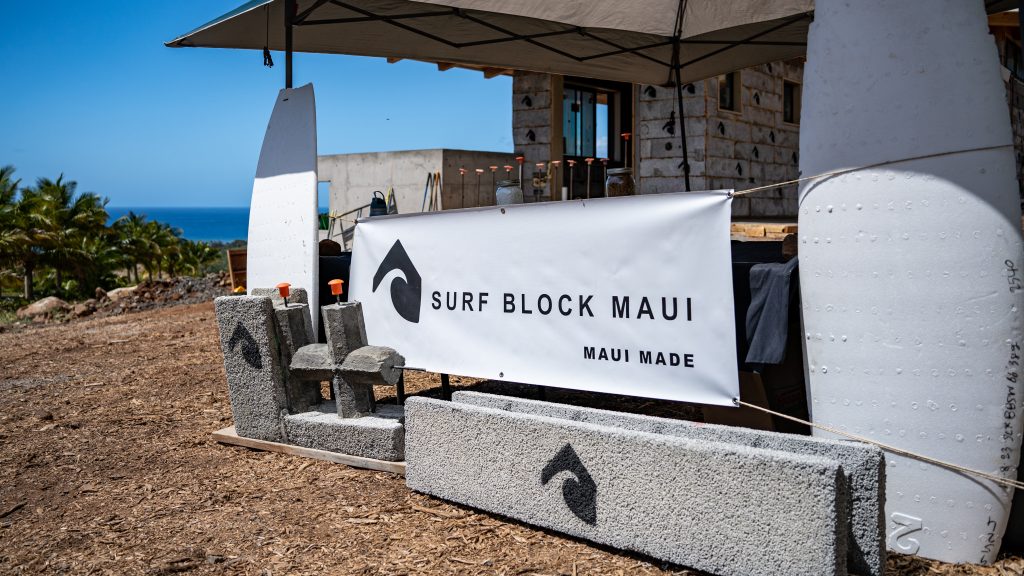
According to Bobby Jewell, Surf Block’s manufacturing lead, it takes only about one to two months’ worth of surfboard waste from Quatro’s flagship store in Haʻikū—home to board shapers Keith Taboul (KT) and Francisco Goya (Goya)—to produce enough material to build a 2,000-square-foot home on Maui.
The concept of “Surf Blocks” was born about eight years ago when David Sellers, an amateur surfer but pro architect, came across a dumpster filled with EPS styrofoam chunks of surfboards outside his office from the neighboring Quatro store. Naturally, Sellers wondered how many houses could be built from it.
The Surf Block system, developed by Sellers’ architecture firm Hawaii Off Grid, takes advantage of a non-wood building material that already exists within the industry, known as Insulated Concrete Forms (ICF), which have long been used for energy-efficient and disaster-resistant construction. Sellers built his first ICF home over a decade ago in the mainland.
Surf Blocks are insulated composite concrete forms (ICCF), which is slightly different. In this case, it means the EPS foam being used to create the outer structure of the block was recycled. The styrofoam Surf Blocks are used to create cast-in-place, steel reinforced concrete walls.
Sellers and Hawaii Off Grid started developing the technology two and a half years ago with the support of a Green Grant from Maui County. Its main purpose was to divert Styrofoam from the landfill, but ever since the 2023 Lahaina wildfires, the blocks have a new appeal: disaster resistance.
Famously, following the Category 5 Hurricane Michael in Florida in 2018, a widely circulated photo showed a lone home still standing amid widespread devastation on New York Times, CNN and the likes. It was an ICF home. Reportedly, the Florida home withstood 150mph winds in what has been called the fourth strongest US tropical cyclone on record.
In addition to protection from high winds, Surf Block Maui claims its product is also non-combustible. With fire resilience becoming a priority for some homeowners on Maui, especially those living in drier leeward areas, Surf Blocks claims to have a competitively priced solution.
Simply put, wood burns; concrete does not. Sellers says the EPS foam wouldn’t ignite but instead would melt if exposed to extreme heat. Evidence shows walls made of “EPScreet” have a 4-hour fire rating as opposed to 15 minutes for a comparable wood-framed wall, a study said.
Recently, one of Hawaii Off Grid’s clients in Olowalu opted to have his ʻohana dwelling “fireproofed.” The ongoing construction project features an off-grid, 1,000 square-foot ʻohana built on approximately 300 exterior Surf Blocks.
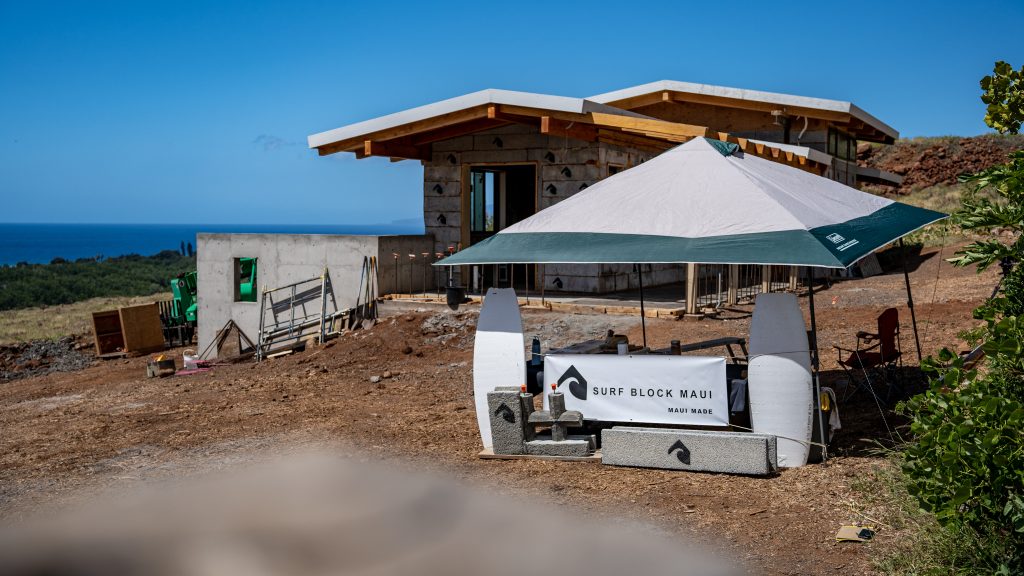
Throughout the worksite mauka of Olowalu on Friday, several Hawaii Off-Grid construction workers praised the rice patty-esque wall forms, saying they preferred Surf Blocks over other materials.
According to Sellers, Surf Blocks are much easier to work with than wood and traditional concrete blocks. “With concrete blocks, you need skilled labor and specialized equipment, but Surf Blocks are lightweight, easy to stack and don’t require the same level of expertise,” he said.
Sellers, who also is on the board of directors for Habitat for Humanity Maui, is even considering volunteer opportunities to build homes with Surf Blocks. He says the blocks present a solution to pervasive labor shortage in the state.
“Even before the LA fires, we have the sixth oldest construction workforce in the United States,” Sellers said. “So this is one of the reasons why we’re looking for solutions that we can build quickly without needing skilled labor, not because we’re against unions, but because we have less labor available.”
A typical Surf Block measures five feet long, one foot tall, and 10 inches wide, making each block significantly larger than traditional 8x8x16 inch “CMU” concrete blocks. One Surf Block covers roughly five square feet of wall compared to one square foot for a CMU block, yet Surf Blocks are still much lighter and easier to handle than a concrete block.
The rough surface of the styrofoam on Surf Blocks also means workers can apply stucco and gypsum plaster directly to the walls without having to provide a lath or scratch surface.
Other than homes, Sellers says Surf Blocks can be used for other load-bearing structures such as retaining walls.
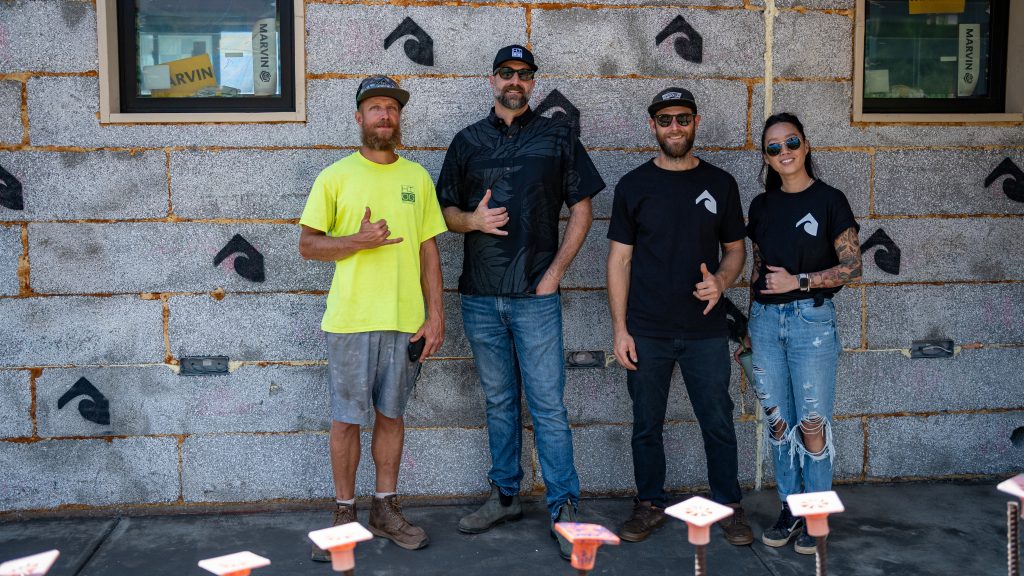
Benefits of Surf Blocks
The idea behind Surf Blocks isn’t just about recycling and ease-of-use; it’s about creating a durable, affordable and environmentally-friendly alternative for home construction. According to Sellers and his team, Surf Blocks have several advantages for homeowners:
- Fire Resistance: Surf Block claims to be a fire resistant building material.
- Mildew and Termite Resistance: Surf Block claims to be mildew and termite resistant, two common issues in tropical climates.
- Effective Acoustic and Thermal Insulation: Surf Block claims to provide twice the insulation value of standard construction materials, with an R-40 wall performance, which exceeds code requirements and has the potential to reduce utility costs and emissions for air conditioning and heating.
- Storm and Earthquake Resistance: Surf Block claims that its walls are five times stronger than wood framed walls.
How it’s made
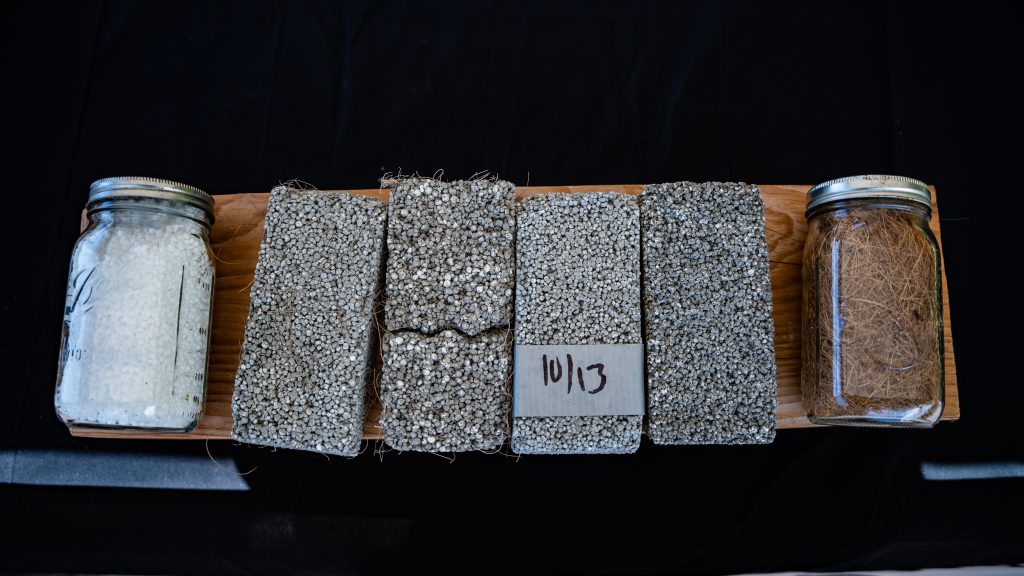
The production of Surf Blocks is surprisingly simple, which keeps costs low and scalability feasible. Sellers’ team can typically produce 10 to 20 blocks per day with just two people, depending on the weather. Given that a 1,000-square-foot house requires about 300 blocks, this production capacity could allow for the creation of 10 to 20 homes annually, assuming a steady stream of surfboard waste from local manufacturers like Quatro.
Sellers and his team use about 50 molds, which are made from reclaimed wood, to shape the blocks. Once the waste styrofoam is ground into pellets using their machine, it’s mixed with concrete and poured into the molds. According to Surf Blocks, the blocks can dry roughly overnight. Two pieces are then glued together and delivered to the construction site. Notably, Jewell reported that one mold can create multiple blocks in a single day.
Cost and scalability
The cost of using Surf Blocks is comparable to traditional building materials, and in some cases, even cheaper. Since the insulation is already built into the blocks, the cost of purchasing and installing additional insulation is eliminated.
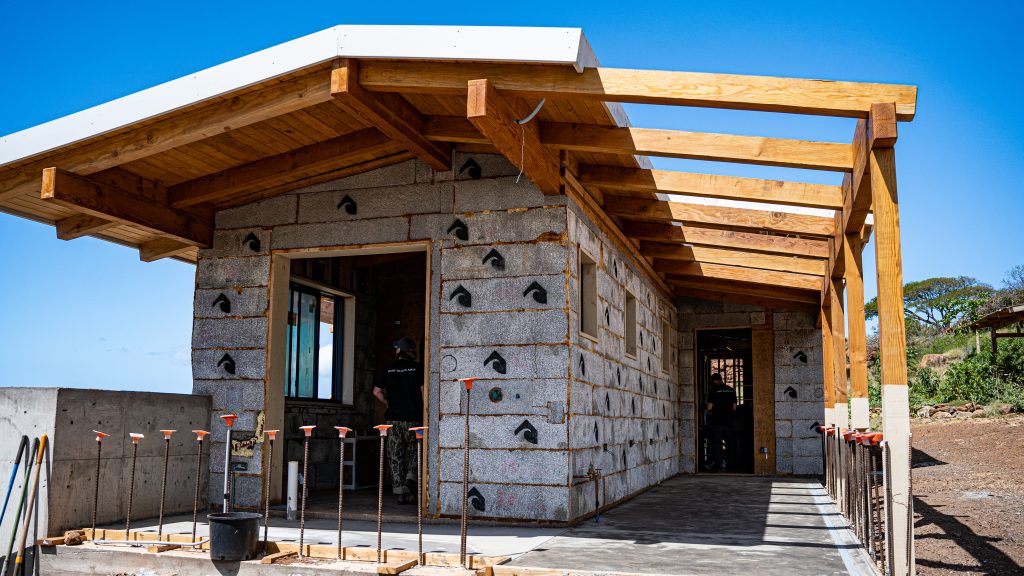
“Right now, one block is costing $42,” Sellers said. “If we scale up and streamline our process, we can bring that cost down.”
As of now, the production of Surf Blocks is limited by the availability of waste from local surfboard manufacturer Quatro. However, Sellers sees potential for scaling up production. “Right now, we’re focused on diverting waste from local surfboard manufacturers, but we’re also exploring other sources of styrofoam waste,” he said. “With the demand in Lahaina and the surrounding areas, we can increase our output by tapping into other industries, like packaging waste from e-commerce shipments.”
Off-grid potential
Surf Block homes are designed to be sustainable and off-grid.
“Everything we use, except for the Portland cement, can be sourced locally,” Sellers explains. “The concrete binding agent is the only component we import, making the overall material significantly more sustainable.”
In fact, Sellers believes that with innovations like algae-based alternatives to Portland cement, it may be possible to completely eliminate the need for imported materials in the future.
Building back Lahaina
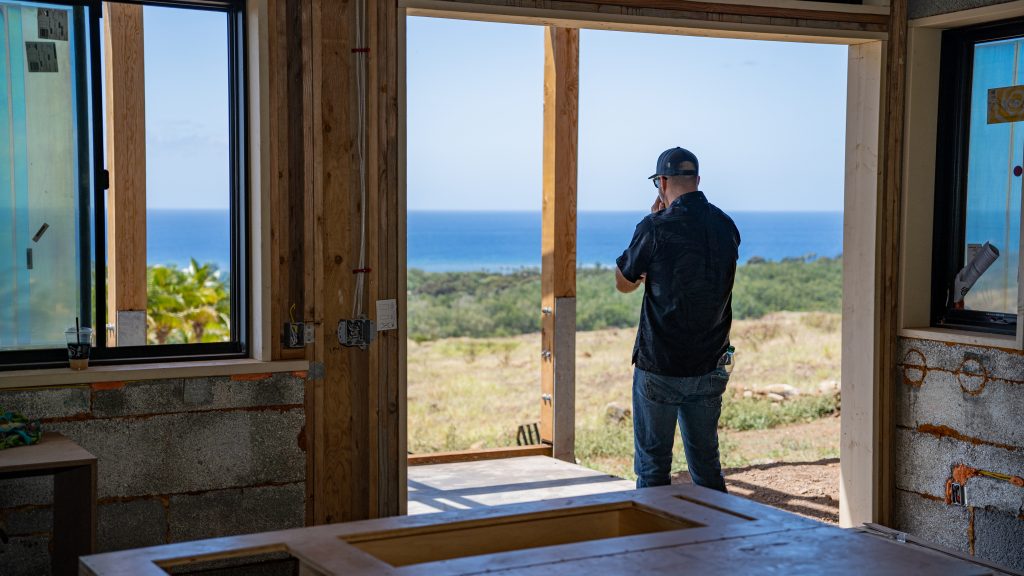
In the wake of the devastating fires in Lahaina, where thousands of homes were destroyed, the demand for quick, sustainable and affordable housing is high. Sellers and his team have already begun the process of building Surf Block homes in the area. “We currently have two homes in the permitting process in Lahaina using Surf Blocks,” Sellers said. “We have the potential to build many more, which is critical given the labor shortages and the overwhelming demand for housing in the region.”
One of the most appealing advantages of Surf Blocks in the rebuilding effort is their speed of construction. The company claims that Surf Block homes can be built faster than traditional concrete block or wood-frame houses, while also requiring less skilled labor.